IPC Disrupts Transportation Infrastructure with Robotics To Help Save Our Nations Bridges
- Doug Thaler
- Jun 5, 2017
- 5 min read
Introduction
Infrastructure Preservation Corporation, “IPC” has disruptive technology that will quickly replace the manual infrastructure inspections conducted today. IPC’s modern technology and robotic inspections provide asset managers (department of transportation) with the critical quantitative data they are actively seeking, allowing for educated and proper allocation of limited budgets, i.e. maintenance dollars. By locating early stage deterioration and benchmarking the status of deterioration over time, the service life of our critical infrastructure can be extended. Untimely replacements will be avoided, saving billions in infrastructure costs.
The Problem:
The infrastructure inspection industry still employs 50-year-old technologies and has had no commercially viable alternative to robotic inspections related to the services IPC is focused on. Due to this subjective methodology, accurate and reliable data on the status of our infrastructure is not available.
Currently bridge decks are still inspected visually and by dragging a chain to listen for differences in sound patterns. Bridge cable stays are being inspected by placing an inspector in a bucket truck at night with a flashlight or are climbed, and cracks are inspected visually with pencil, paper, and a crack measurement ruler. Infrastructure is currently in a state of disrepair; DOT budgets are tightening and the world’s economic viability and competitiveness depends on the health of its infrastructure.
The Solution:
IPC has 5 patents with 3 more in process. IPC’s technology provides thorough inspections with true imaging and accurate benchmarking with a detailed record of ongoing results. Moreover, this higher quality of data is performed at a lower cost point. Of specific interest to the DOTs is the avoidance of lane closures and boom trucks. Locating early stage deterioration and making repairs in a timely manner will not only help better protect the public’s safety but extend the life of critical infrastructure assets. This will save hundreds of millions of dollars in emergency repairs and billions in untimely replacements.
BridgeScan® Complete Bridge Deck & Approach way Inspection
Provides internal imaging of the bridge deck and approach roadways. This is a 100% inspection of a bridge deck locating and quantifying deterioration and corrosion. IPC locates delamination, deboning, rebar placement, voids, water intrusion and cracks. IPC reporting provides actionable items so the DOT knows the size and severity of deterioration and can plan accordingly.
Current inspections of bridge decks are comprised of dragging a chain across part of a bridge deck and listening for changes in the sound. These inspections are conducted while traffic is flying across the bridge at 70 mph.
Current Inspection Method IPC BridgeScan® Bridge Inspection Method


PoleScan® Patented
Current HMLP Inspection Method | IPC’s PoleScan® High Mast Light Pole Inspection Method


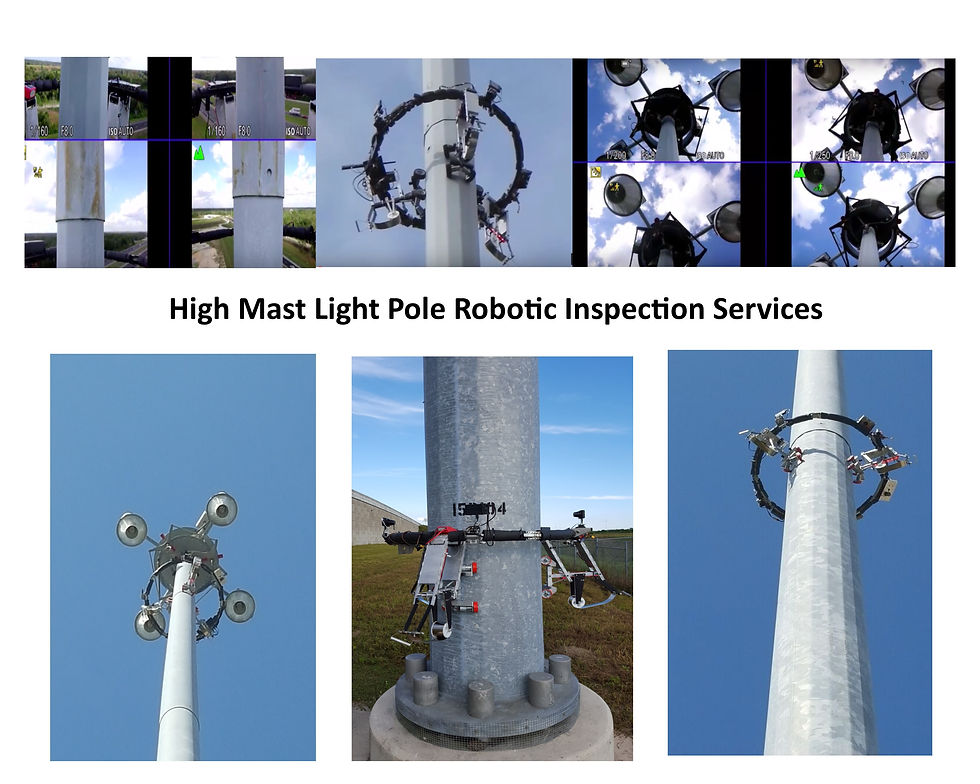
A robotic device providing inspection date for High Mast Light Poles along highways and interstates. These inspections take place every five years. IPC’s HMLP inspection robot ascends and descends high mast light poles providing high definition video and stills of all issues on the pole, seams and luminaries as well as the position on the pole where these issues exist. It also uses LIDAR to measure the length, width and depth of cracks as well as ultrasonic for thickness measurement.
IPC also conducts ultrasonic testing of the anchor bolts that go down into the ground three feet and tend to corrode and crack due to high winds and stress. All data is recorded to monitor any progression of problem areas over time. Today an inspector conducts these inspections on the ground with a pair of binoculars and a pad and paper.
PoleScan-R is a repair robotic device that preforms minor repairs.
TendonScan® Post Tendon Tendon Inspection Services
External post tension tendons hold up our nations bridges and highway on-ramps and off-ramps. There are millions of miles of post tension tendons worldwide with no commercially viable economical way to inspect them until IPC. TendonScan® is composed of two units: 1) Peers through post tension tendons locates and quantifies corrosion and 2) locates and quantifies air, water & bleeding grout which are precursors to corrosion development.
Current inspection methods are visual using flashlights or hit a tendon with a hammer to listen for differences in sound.
Current Inspection method IPC’s TendonScan® Bridge Inspection Method

Post Tension Tendon Inspections
CrackScan® Concrete & Steel Crack Inspections
CrackScan® is a laser inspection method that locates cracks in concrete and steel structures. It creates 2D and 3D crack maps that show length, width of cracks as well as their position on the structure. A recorded history is kept to monitor for progression over time. All this is accomplished without lane closures or bucket trucks.
Current inspections use an inspector in a bucket truck with lane closures for visual inspections. A double-blind study on two bridges resulted in the engineering firm finding a total of three cracks on both bridges and IPCs CrackScan® inspection system found 23 cracks on both bridges. The firm then verified IPCs results.
Current Inspection Method IPC’s CrackScan® Concrete Crack Bridge Inspection


CableScan®
CableScan® Bridge Cable Stay Inspection Service provides a 360-degree inspection of cable stays without lane closures or boom trucks. It records high definition video and stills. All issues are recorded and photographed as well as the position along the stay and deck. LIDAR is used to measures cracks and is wireless controlled from the ground.
Currently inspections require lane closures and bucket trucks or inspectors climbing the stays while visually inspecting what they can see.
A previous conventional inspection of an 84-stay bridge found one problem. IPC performed a QC of that inspection and found 12 issues on 9 of the 84 stays. In addition, during the inspection with the traditional method using lane closures, 6 accidents occurred over a 12-week period.
Current Inspection Method IPC’s CableScan® Inspection Method
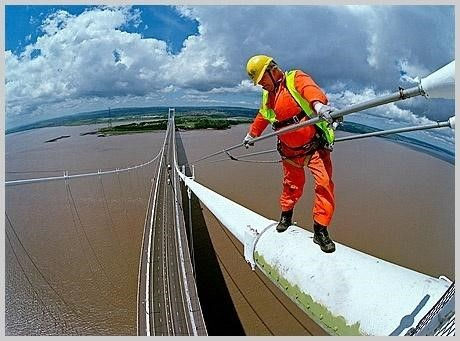

CableScan®-R is a repair robotic system that makes minor repairs without lane closures or boom trucks.
ColumnScan®
A robotic inspection system that inspects the inside of bridge columns on complex bridges. It lowers into columns and inspects the interior of the columns with LIDAR, high definition video and stills. It transmits information to a surface station for onsite evaluation. It’s equipped with extending and reticulation arms to maneuver and record around obstructions.

Currently an inspector is lowered into a column with a helmet flashlight, pad and paper.
The robotic inspection services IPC provides not only replaces current inspection methods but provides superior results over these methods. IPC’s robotic services are safer for the public, safer for the inspector and do not require lane closures or boom trucks for many of our inspections.
Manual method of inspecting a bridge column.
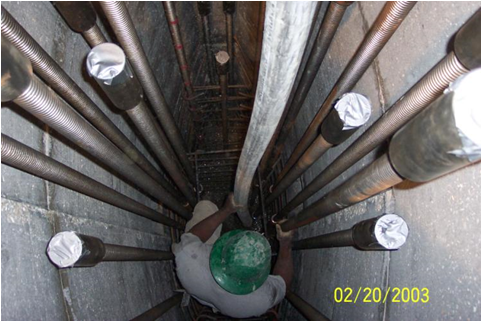
*Dangerous
*Typically inspector requires oxygen
IPC's robotic inspection does not require danger to an inspector.
Provides high definition video and infrared to locate deficiencies and report on them. For more information contact
727-372-2900 ext.24 or info@infrastructurepc.com
コメント