Improving Post Tension Cable Inspections
- Doug Thaler
- Oct 6, 2016
- 4 min read
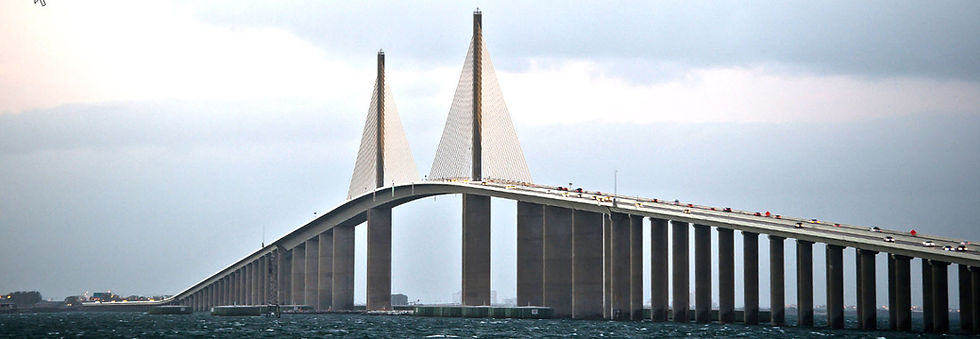
Post tension cables are used to help support our bridges and roadways. Millions of miles of these steel cables embedded in grout and surrounded by an exterior coating are helping to hold up our bridges and roadways. Even there is a certain amount of redundancy built into all of our vital infrastructure assets, we are still inspecting them the same way that we inspected them 50 years ago. Primarily this consists of a visual inspection or by hitting the cable with a hammer to listen for tone differences. There are experts in inspecting tendons listening for tone differences that are very good at locating problem areas but after 50 years of doing things the same way, with technology where it is today, isn't it time that we updated the way in which we inspect our bridges and roadways.
Shouldn't we be adopting robotics and modern technology just like every other industry has to make our infrastructure safer. Doesn't modernization typically offer better results in a more cost effective manner and wouldn't better inspection results aid in extending the lives of our critical infrastructure assets.
If 10 inspectors conducted the same inspection do you think we would get 10 of the exact same results or different?
Our nations infrastructure is relying on this 50 year old inspection method to keep us safe.
With our infrastructure deteriorating at a faster pace than we are funding repairs we need to improve early detection of deterioration. Using
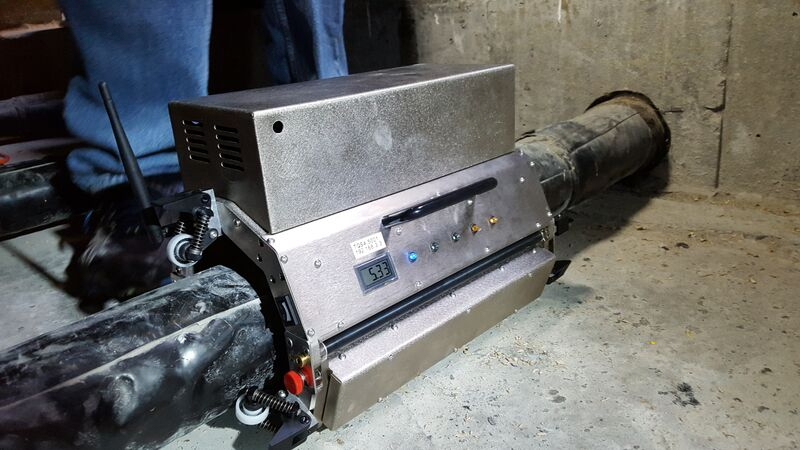
nondestructive "NDT" testing methods and nondestructive evaluation "NDE", we can today locate the areas of concern, its size and shape prior to drilling into a tendon or utilizing destructive methods. Once you drill into a tendon, you expose the internal tendon to additional air and moisture which hastens deterioration.
IPC, (Infrastructure Preservation Corporation) a Florida based robotic engineering company has developed a tendon scanner that can locate the pre-cursors to corrosion within a post tendon cable, air, water and bleeding grout. By viewing the inside of the tendon we can see the size and shape of the anomaly and repair with pinpoint accuracy.
A study examining a number of inspection methods prior to IPC compared a number of NDE (Nondestructive Evaluation methods and NDT (Nondestructive Testing) inspection methods and concluded that their was no viable method to properly inspect bridge tendons. "

According to a report published by the Federal Highway Administration (FHWA) in 1998 the cost of corrosion in highway bridges in the U.S. was estimated to be $8.3 billion a year. (FHWA 2001).
The report further claimed that:
"The owners of concrete bridges with various steel elements, especially with pre-tensioned or post-tension bridges, in the US and abroad face a serious problem. They have the responsibility of ensuring public safety , but have no means to effectively detect corrosion in these bridges" that is until now. You can read the full study here.
Infrastructure Preservation Corporation spent 6 years developing TendonScan™ which inspects post tension cables with an MRI like (X-Ray) image of the inside of a post tension cable.

Both pictures to the left and above show an actual post tension-ed cable. That is a steel cable embedded in grout and sealed with a rubberized exterior. Air and moisture intruded into the tendon causing corrosion and eventually for the cable to collapse under stress.
Thankfully there was enough redundancy on the bridge so the bridge did not collapse. We may not be so lucky next time.
Inspection methods with IPC (Infastructure Preservation Corporation) will allow you to look inside the tendon and see if air or water has intruded. IPC can produce a 3d image showing the placement of the intrusion within the tendon. By doing so we will be able to make repairs in a more cost effective and efficient manner and extend the life of these assets while insuring their safety for the public. IPC, a Florida based robotic engineering company

has developed a tendon scanner named TendonScan that can locate the pre-cursors to corrosion within a post tendon cable, air, water and bleeding grout. Asset managers can then be directed to the exact location of the abnormality and repair it before it becomes too late.
Bridge inspections are required by the federal government to be conducted on every bridge every two years. If a bridge is deemed structurally deficient it needs to be inspected every year. As anomalies are encountered repairs can be scheduled on a timely basis. This would help with both budgeting and scheduling for the asset manager and insuring that the bridge and the public were safe.
For IPC Infrastructure Preservation Corporation the road to correcting our infrastructure begins with updating the inspection methods. By providing more detailed inspections and locating early stage deterioration, we can save billions in infrastructure asset replacements and make our existing infrastructure safer for the public and the inspections safer for the inspector. The fact that modernizing inspections does not require heavy equipment or lane closures is just an added benefit.
Comments